- Product
- Liquid Filling Machine Series
Product Details
Aseptic Filling, Stoppering & Closing Machine (Vial / Eye-Drop)
Product Introduction
KDL-980EU Aseptic Filling, Stoppering & Closing Machine (Vial / Eye-Drop)
GENERAL:
Kwang Dah accumulated a lot of producing experience in liquid filling, stoppering & closing machine for many years. We developed the In-Line Aseptic Preparation Machine which is designed for vials & eye-drops.
It can be equipped with unscrambler, nitrogen filling, liquid filling, stoppering, pre-closing, & closing machine become a complete In-Line eye drop processing machine.
It also can equipped with turn table, nitrogen filling, liquid filling, rubber stoppering & aluminum cap closing machine become a complete In-Line vials processing machine.
In accordance with PIC/S GMP & Aseptic Preparation requirements, machine using many high precision servo controllers & combined PLC & HMI for production operation & adjustment, therefore “ONE TOUCH” will automatically adjust the conditions of production during production operation or adjusting, it is a user-friendly with high-efficiency machines.
Max. Capacity: 100 Bottles/Minute.
FEATURES:
- The housing and surface are covered with stainless steel. All liquid contact parts are made from stainless steel 316, meeting the standards of PIC/S GMP & cGMP.
- KDL-980EU is monoblock designed & it is automatic filling, stoppering & link with closing machine for vials & eye drops.
- In order to meet Aseptic Preparation standard, it is without any pneumatic components & adopted mechanical transmission with servo motor PLC controller & HMI to enable the function of working station more accuracy & easier for operation the machine.
- The special fence is designed for reject the falling down bottles automatically before get into star wheel to make the production process more smoothly.
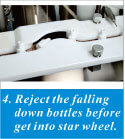
- Equipped 2 separate star wheels in front & rear of the center working star wheel to ensure the bottles in & out smoothly.
- The bottles transfer guide & star wheel are made from engineering plastic & they are easy to clean & change over without any tooling to achieve high efficiency of production operation.
- It equipped 12 precision servo motors to enable the function of filling, stoppering, pre-closing & reject device more accuracy.
- Two stages filling system prevents liquid spilling out during high speed filling.
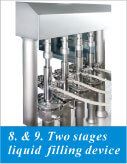
- The filling volume (piston stroke) controlled by servo motor, it can fine adjust for volume. The filling volume is very accuracy. (within +/- 0.5%)
- The liquid filler can fill the liquid from bottom of bottle with gradual upward movement to prevent liquid spills out and the forming of foam.
- It adopted the servo motor for filling nozzle upward & downward, it can be adjusted the speed of upward for different products.
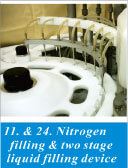
- It adopted the mechanical design with servo motor to grab the stopper or rubber stopper into bottles precisely.
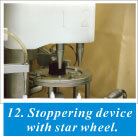
- It adopted the mechanical design with servo motor to grab caps on the bottles precisely. It is convenient for operating & adjusting.
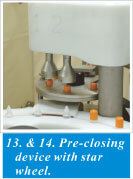
- It equipped pre-closing device to avoid the cap falling down during transporting & avoid the contamination from generated the dust due to the friction during tighten the cap.
- Equipped with a torque limiter under the center working star wheel, in case of crash on the star wheel, machine will stop automatically to protect the index device.
- The filling piston & cylinder are 316 stainless steel, both piston and cylinder are one-piece machining made without welding to ensure clean & no residue remains.
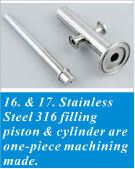
- The piston & cylinder are hard chrome plating & precision polishing for increase the filling accuracy & life time.
- In order to achieve Aseptic Preparation standard, it equipped the isolation section for supplement the stopper during production to avoid the external sources of contamination into the clean area.
- It equipped the automatic supplement caps device to keep away the possibility of causing contamination for supplement caps manually.
- All contact with liquid material parts can be executed 121oC sterilization procedure over 40 minutes.
- This machine is controlled by PLC, it can detect the products & function as below:
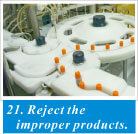
- If no bottles are fed then no liquid is filled.
- If no liquid is fed then no stoppers are inserted.
- If no stoppers are inserted then no caps are closed.
- Machine will reject the improper product automatically.
- Adopt transparent safety guard (made of glass or PC material) & specifically designed for isolation gloves (Option) to prevent the contaminated.
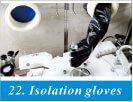
- The machines can be equipped with laminar air flow for operations requiring a particle-free and clean air environment. (Option).
APPLICATION:
The operation sequence & description of stations:
Related Products
Liquid Filing, Plugging, & Capping Machine
Max. Capacity: 50~100 Bottles/Minute.
This KDL-980 series machine is an automatic liquid filling, plugging, & capping machine.
It is capable of filling small containers (2cc to 60cc) including eye-drops, vials, cosmetics, & other types containers.
This non-black type machine consist of bottle feeding, nitrogen air filling, liquid filling, plugging, and capping.
Liquid Filing, Plugging, & Capping Machine
Max. Capacity: 50~100 Bottles/Minute.
This KDL-980SG machine is an automatic liquid filling, plugging & capping machine.
It is capable of filling small containers ( 2cc to 100cc ) including eye-drops, vials, cosmetics, & other types containers. This non-block type machine consist of bottle feeding, nitrogen air filling, liquid filling, plugging, and capping.
Suitable for pharmaceutical, cosmetic, nutrition, Food industries etc.